Metlab offers black oxide coating service. This service is in addition to its current array of heat treating services.
Black oxide, which can be applied to a broad range of products, is classified as a conversion coating. It can be applied to ferrous materials as well as stainless steel, copper, copper based alloys, zinc, and sealed powder metal. It can also be used to blacken silver solder.
Black oxide imparts a deep, black, lustrous appearance to the parts being coated, and replicates the surface finish of the part. Although black oxide provides mild corrosion protection to the treated parts, it is primarily used because of its aesthetic properties.
When black oxide is applied to most materials, a top layer of oil, which is generally dry to the touch, wax or lacquer, is applied to enhance the corrosion properties. A further advantage black oxide has over other coatings, is that as a conversion coating, there is minimal buildup, which can generally be measured in microns.
Black oxide can be applied through either a hot process or a cold process. Metlab only performs the hot process as it is more cost effective, provides superior coverage over the cold process and offers enhanced corrosion protection.
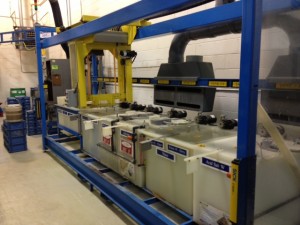 Automated black oxide line. Parts move from tank to tank automatically using a robotic handler. (Photograph is courtesy of Hubbard Hall)
The process starts by fixturing the parts. Fixturing consists of hanging individual pieces from a wire, placing parts in baskets, or putting them in a tumbler, depending on part geometry. For example, large unwieldy parts are hung individually; machined parts, which could become damaged from excessive handling, are placed in baskets, and small parts like nuts, bolts and washers are generally tumbled.
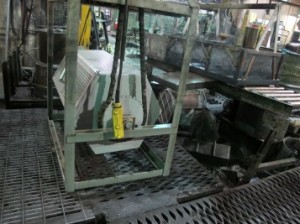 Chain driven motorized tumbler for holding small machined parts like fasteners to be blackened.
The fixtured parts are first cleaned by submersion in an alkaline bath, and then rinsed in clean water. If necessary, parts are moved to an acid bath, and then rinsed again in clean water. For blackening ferrous pieces, parts are placed in a bath of proprietary blackening solution. The blackening solution, which contains sodium hydroxide, nitrates and nitrites, converts the surface of the material into magnetite (Fe3O4). Hot black oxide for stainless steel parts consists of the same steps, except for the proprietary blackening bath.
Because stainless steels have a tightly adhered oxide layer, it is critical to break through this layer in order to ensure that the surface consists of free iron for conversion. Although breaking the layer can be done chemically, it is generally done through the use of glass bead blasting or sandblasting because those two methods are more efficient. Oil is typically applied to the blackened surface to impart a high degree of luster, unless a matte finish is desired, as in the case of medical instruments.
However, regardless of the material being blackened, all of the cleaning and rinsing is done in warm baths, up to 160°F, and the blackening at 265°F to 285°F.
The final step in the process is applying oil to the heated parts. This oil, which is generally evaporative and dry to the touch, seals the black finish by “sinking” into the applied porous layer of the black oxide. It is the oil that provides the corrosion protection the work-piece.
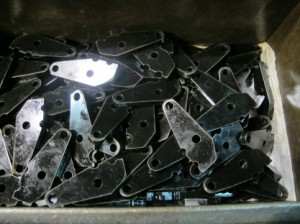 Assortment of jaws, black oxide finished and oiled ready for assembly.
The end result – Cable cutters with black oxide finish on the jaws for enhanced aesthetics as well as improved corrosion protection
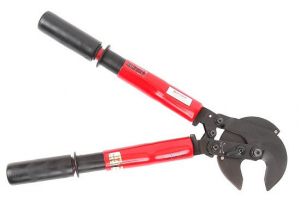 (Photo courtesy of Electroline Inc.)
The black oxide process has many advantages over other processes. These include:
- Economics – Black oxide is far less expensive than painting, electroplating or powder coating.
- Productivity – blackening can be done to large batches of parts by tumbling or fixturing, making it ideal for processing small parts.
- Size Change – There are no significant dimensional changes to a black oxide part. The layer thickness depth can be measured approximately one micron.
- Specifications – Black oxide conforms to several different military specifications, including MIL-DTL-13924, as well AMS 2485, ASTM D769, and ISO 11408.
Black oxide finishing is used for a variety of industrial applications in widespread industries. Some examples include:
- Retail: Store displays and fixtures.
- Automotive: Cans for oil filters, numerous under the hood fasteners
- Electrical: Wire strippers and cutters
- Home / Garden: Tree toppers – jaws and clipping tools
- Gearing: Small gears for tiny timers and electrical switches
- Firearms: Gun components, shotgun shell magazines
Posted in Black Oxide
|
Tagged Black Oxide
|
Metlab has received two contracts from defense contractors to heat treat tank components. The contract is part of an ongoing multi-year program supported in part by US funding. Metlab was selected for this program due to its unique heat treating capabilities for processing large components.
The first contract was received from an Israeli defense company to nitride turret gear races. These gears, with teeth on one side that mesh with smaller gears, and a bearing race on the other allow the tank turret to rotate 360°. The gear race is made from a European steel similar to Nitralloy 135M. Each gear race is over 8′ in diameter. The parts are masked with to allow certain non-working areas of the gear races to be machined after heat treatment. Parts are heat treated in one of two of Metlab large furnaces, the largest measuring 15′ in diameter by 12′ deep, and 20 or more rings can be accommodated in a single 120 hour cycle.

Merkava IV main battle tank used by the IDF forces in Israel. The Merkava tank has been in production since 1979 with the fourth generation model manufactured since 2004.
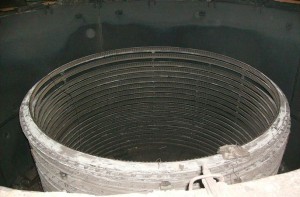
Load of tank turret gear races after completion of the nitriding cycle shown ready for removal from Metlab’s large diameter pit furnace. Flaky material on the outside and top surfaces of the gear races is stop off paint used to keep these surfaces soft.
On the current tank turret gear race program, Metlab has heat treated over 1,200 parts. Nitriding was selected as the preferred process over flame hardening, due to its ability to produce consistent, accurate hardening results with no component distortion. Since the change from flame hardening to nitriding, there have been no field failures of any of the components heat treated by Metlab.
The furnaces used for nitriding the tank turret gear races were originally designed and manufactured to nitride ship and submarine gears for the U. S. Navy. Typical drive gears measure over 10′ in diameter by 10′ tall, and weigh in excess of 12,000 pounds each. Over 50 of these gears were nitrided on the original project.
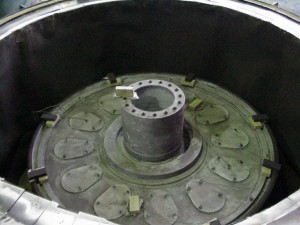
Typical main propulsion drive gear for a submarine/destroyer nitrided by Metlab, shown at the end of the heat treatment cycle, ready for removal. Post heat treatment processes include inspection to ensure that hardness and case depth requirements have been met as well as sandblast cleaning to remove stop off paint from all protected surfaces.
The most recent contract received by Metlab is from a domestic supplier for heat treating tank track connecting pins for the same Israeli defense company. Parts are manufactured from 4140 steel hex bar and measure about 3/4″ in diameter by 14 3/4″ long. The parts connect the individual tank segments together forming a continuous loop which rides on the sprockets. They are heat treated to a hardness of HRC 30 – 36 and must be held straight within 0.015″ over the complete length of the bar.
The contract is for over 150,000 connecting pins; Metlab delivered about half of that quantity in 2014, and the balance is due within the first half of 2015. In addition to the above two contracts, other parts processed for tanks include the induction hardened tank sprockets, road wheels and idler drive gears.
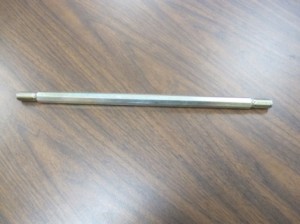
Finished track connecting pin heat treated by Metlab showing threads and plating in place.
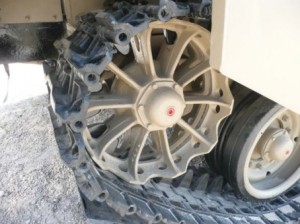
Tank tracks in place engaged with sprocket and road wheel. Each track segment is connected to the adjacent track segment using a connecting pin heat treated by Metlab.
Metlab has for many years processed numerous other military products including induction hardened tank sprockets, road wheels and idler drive gears, and has been a significant part of the military support effort.
As Metlab continues to grow the company is adding more capacity and fleet services to accommodate customers. Recently the company added a 26 foot Box Truck that can haul up to 26,000 GVW. This is in addition to several other trucks and vans that allows the servicing of routes throughout an area within a 100 mile radius of the heat treat facility as well as parts of Maryland and New Jersey for pickups and deliveries. The new box truck is also a strategic addition to the company to compliment the amount of projects for Metlab’s new Vacuum Furnace installation.
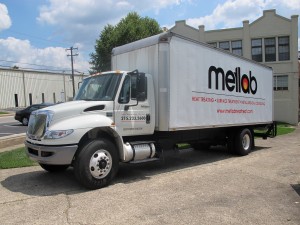
The new VFS – HL34 furnace was added in August to accommodate the demand for heat treating stainless and tool steels and high temp nickel based alloys. This vacuum furnace compliments an existing smaller furnace and has a work zone approximately 24″ wide x 48″ deep x 24″ high.
The increased capacities allows for processing new materials and a wide range of part sizes.
• Tools and dies
• Stainless Steel Tubing
• Aerospace jet engine parts
• Medical parts
Currently Metlab is running three shifts on the new vacuum furnace.
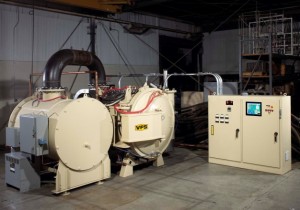
Metlab offers vacuum heat treating of stainless steel, nickel base super alloys, tool and die steels, as well as parts made from other materials like titanium and copper based alloys. The equipment used by Metlab has an all metal (molybdenum) hot zone in a stainless steel water cooled chamber, high vacuum diffusion pump system, current proportioned power supply for controlled heating, state of the art microprocessor controls to allow for automatic temperature and vacuum control, and repeatability. The furnace is rated for a maximum 2400°F operation, at a vacuum level of 10-5 Torr. Applications for the furnace include bright annealing and hardening of tool and die steel molds and dies, heat treating stainless steel medical instruments and implants like hips and knees, age or precipitation hardening of 17-4 PH, 15-5 PH or 13-8 Mo Stainless Steels, and other processes where clean, scale and decarb free surfaces are required.
Benefits
• Nominal surface oxidation or discoloration
• Minimal part distortion
• No post cleaning operations
• Near finished, machined shape prior to treatment
Vacuum Furnace Applications:
• Hardening
• Annealing
• Normalizing
• Solution Treating up to 2400°F
The vacuum furnace operator and Metlab’s electrical engineer have been to Ipsen University training in Rockford, Illinois for operations and maintenance training. Ipsen U is a practical course for building and refreshing knowledge of vacuum thermal processing equipment specifically the VFS furnace that Metlab just acquired.
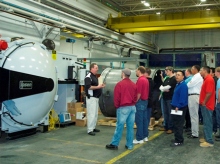
Ipsen U addresses all levels of experience and is geared specifically for the two Metlab employees who attended. They were encouraged to ask questions about their furnaces and applications, and some of the maintenance and technical issues that they encountered on equipment startup. The class they attended followed a format that allowed them to interact with several Ipsen maintenance and technical experts and have their specific questions answered as well as hands-on operation of similar furnaces and maintenance procedures.
This past spring, Metlab assisted Penn Electric Racing by heat treating one of their critical drive train components. Penn Electric Racing is part of a colligate international competition; similar to an Indy stock car race where the teams must design and build a car from the ground up. The design and build must be completed in nine months in order to enter the competition. Metlab sponsors the University of Pennsylvania’s racing team each year and provides free heat treating and also manufacturing consulting services to the team by connecting them with various material and machining suppliers. The racing team prominently features a Metlab sticker showing their support on the car.
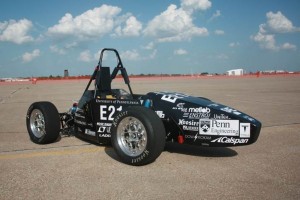
Students on the team design, fabricate, and compete with small formula-style race cars. Restrictions are placed on the car frame and engine so the students’ knowledge, creativity, and imagination are tested. Four cycle engines up to 610 cc can be turbocharged or supercharged, or up to 85 kW of electric motors add a new dimension to the challenge of engine design. The vehicles are judged in three different categories: static inspection and engineering design, solo performance trials, and high-performance track endurance.
“This is the first time we had a running car for the Electric SAE competition” comments Tommy Sutton of the Penn Electric Racing Team. “However, it was not able to race due to technical inspection issues. Instead we ran the car on an open track. For next year, we hope to optimize the car for performance and safety so that it will be able to pass inspection, compete, and place highly among the field.”
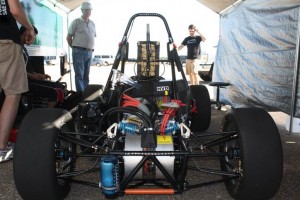
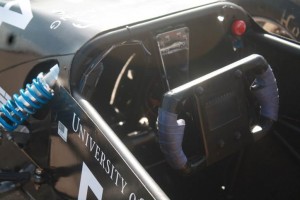
Other members of the team include team captain Adam Farabaugh, Manfred Reiche, John Doyle, Foster Collins, Parth Patel, and Aedhan Loomis, among others. Out of twenty teams that entered the 2014 Lincoln FSAE Electric competition, only three passed the stringent regulations for the competition.
The race events include:
• Auto Cross
• Endurance Race
• Skip Pad
• Acceleration
“Our goal was to design the drive train such that the rear spindles could bear both braking force as well as the motor torque” Sutton elaborates. “We wanted to have the brake rotor integrated into this system. The design and implementation became a very complicated task. The spindle was internally manufactured by the team and brought to Metlab for heat treatment. The design parameters called for a final hardness of HRC 40 – 42. The parts came out well with minimal distortion, hence very little post-machining required. Consequently the installation of the spindles went well.”
Metlab has a policy of providing heat treat and surface finishing services to various universities and colleges at no cost. Other projects have included the stress relieving of racing car frames for a race car prepared by Drexel University as well as heat treating aluminum rocket tanks for Boston University. It also, from time to time, hires interns and Co-Op students from local Universities, providing them with on-the-job practical experience to help further their professional education.
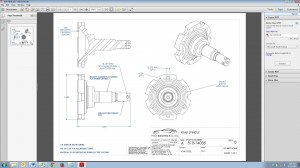
Sutton summarizes, “I just wanted to express everyone’s thanks for Metlab’s sponsorship of our team this year. It was an enormous success for us with our first Formula SAE Electric car, and a tremendous learning opportunity for us to expand upon for next year. We are all confident that our car next year will be able to place at the top of the podium given our current platform we have established this year. The spindles worked excellently for us! The heat treating was pivotal for their success.”
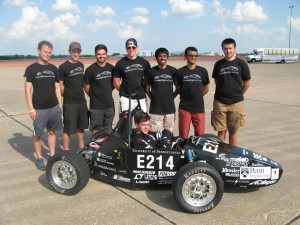
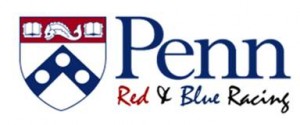
Metlab Heat Treating is able to process a wide variety of parts in small sizes. The company is well known for large part heat treating; however the company maintains a long history of small parts applications.
Watch the Small Parts Video to see more examples and capabilities:
Here are some Small Part examples along with the treatment process:
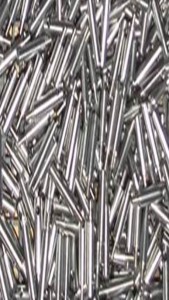 Low Carbon Steel Pins – Case Hardened
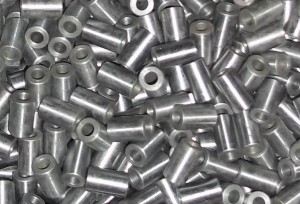 8620 Steel Bushings for Carburizing
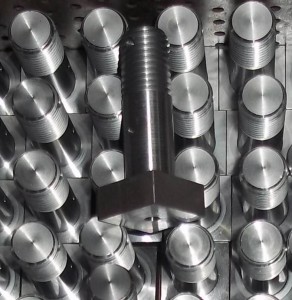 420 Stainless Steel Bolts for Vacuum Heat Treating
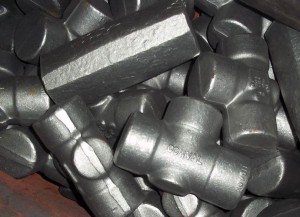 Stainless Steel T’s, Solution Treat and Age Harden
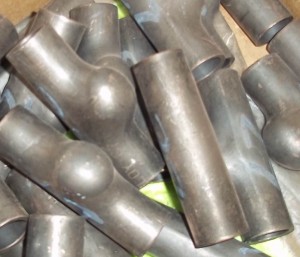 Stainless Steel Fittings
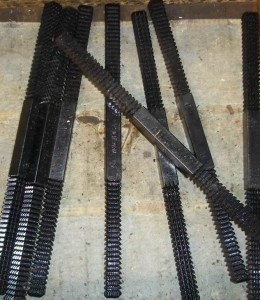 Steel Files: Heat Treated and Black Oxide Finished
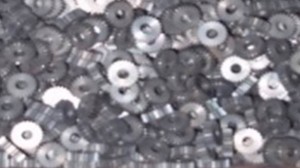 Automatic Timer Small Gears: Hardened & Tempered
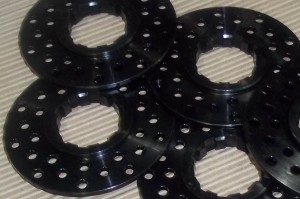 4340 Clutch Hubs: Heat Treated & Black Oxide
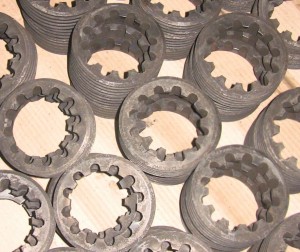 Grey Cast Iron Slips: Induction Hardened to HRC 50
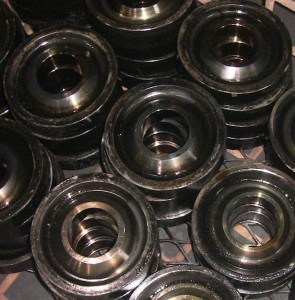 Crane Wheels: Flame Hardened To Toughen Rims
One of Metlab’s customers in the South shut down their heat treat equipment for major repairs. The furnaces are expected be down for about four weeks. Their product is gears and pinions, ranging from ¼ pound to about 50 pounds in weight, physical size about 2” in diameter to 60” in diameter, 1” to 24” thick. They also make pinion shafts, and their customers are industrial manufacturers of motors, transmissions, hand tools and a general cross section of power transmission equipment.
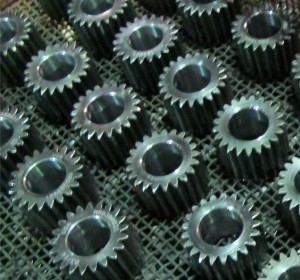
When not in a shutdown mode, this manufacturer offloads their over-capacity to Metlab as well as their large size gears which they cannot process themselves, particularly nitriding and carburizing and hardening of large power transmission gears. During their shut down, they off load their entire production to Metlab because of our furnace capacity, flexibility, quality and ability to process multiple batches quickly.
Metlab essentially serves as their in-house heat treat source. While many customers think of Metlab as a large gear heat treat company, this is not the only area of expertise as evidenced by the ability to step in and assume this role for customers who require smaller part processing.
During this shut-down period, Metlab is expected to heat treat about 4,000 pounds of product a week for this customer, processing 4320, 8620, 9310 carburizing grades of gears and pinions with requirements for shallow effective case depths ranging from 0.010 – 0.020” to deeper case depths up to 0.100 – 0.125” case depths.
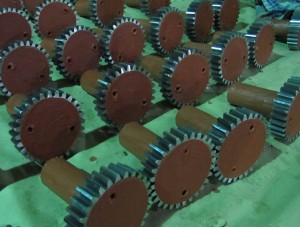
Some of these gears and pinions require masking to prevent areas which require post-heat treatment machining from becoming hardened as well as cryogenic processing and multiple tempering as part of their process. In addition, a portion of the product processed will be straight hardening and tempering of 4140 and 4340 gearing.
To expedite the heat treating process Metlab receives the purchase orders and packing slips from the customer as soon as the parts are in the customer’s loading dock, allowing for the detailed process specification and shop travelers to be prepared ahead of time, so that the parts are married up with the receiving paperwork when they arrive.
This allows the work to be scheduled well in advance accommodating the just-in-time work flow required to keep the production flow going. Likewise, shipping documentation, including packing slips and certifications for case depth, hardness and microstructure are e-mailed to the customer’s receiving and quality control department so parts are received in advance, minimizing waiting time for paperwork to catch up to the appropriate personnel.
This customer is located about 750 miles away from Metlab, making it a one day point for shipping, and as the cost of freight is minimal, the economics are strongly in favor of outsourcing the heat treating.
Metlab, a leader in the supply of heat-treating and surface treatment services, based in Philadelphia, announces the acquisition of a fleet of new vehicles and expanded pick-up and delivery service.
Metlab currently operates:
• 26’ box truck, which is 25,000 GVW
• 24’ box truck
• Access to stake body truck
The company has invested in new vehicles to provide extensive, reliable service:
• A new 16’ box truck- 12,500 GVW
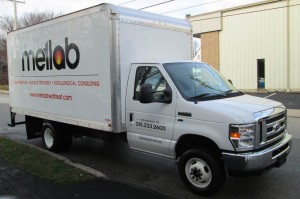
• A new 1-ton van. To kick-off our Baltimore runs and complement our overall pick-up and delivery service.
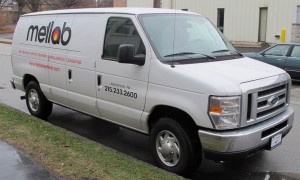
Daily pick-up and delivery is available to companies in the following regions:
• Philadelphia,
• Montgomery,
• Bucks County regions
• New Jersey
Pickup and delivery is now available Twice A Week for:
• Allentown
• Bethlehem
• Baltimore and surrounding areas
• Delaware
• Northern New Jersey
There is typically no charge for our pick-up and delivery service. Drivers are equipped with two-way radios and cell phones to allow for immediate, last minute requests for service.
Due to our large volume shipping we receive excellent freight rates from common carriers and are often able to arrange freight either by LTL or flat beds pass along prepay and add freight charges, passing along significant savings to our customers.
Customers either issue us purchase orders, or we provide them with a pad that they can keep in the shipping and receiving department for their use to write up individual orders for heat treating and surface finishing.
Metlab provides:
• Hardening
• Tempering
• Carburizing (case-hardening)
• Nitriding
• Annealing
• Black oxide
• Induction/flame hardening
• Stress relieving
• Cryogenic treatment and other thermal processes.
Materials processed include all ferrous and non-ferrous materials. Heat treating is done in strict accordance with military specifications.
Please call our toll free number, 1-800-319-7359 to schedule a pick-up.
Mark Podob
Vice President, Marketing and Sales
Metlab
1000 E. Mermaid Lane
Wyndmoor, PA 19038
215-233-2600 Ext. 232
(F) 215-233-5653
mpodob@metlabheattreat.com
When customers think of Metlab, they think of large parts heat treating. But Metlab has a long history of heat treating small parts as well. With the acquisition of the John V. Potero Company in 2001, moving it from Philadelphia a 10,000 square foot facility in downtown Philadelphia to the Metlab campus in Wyndmoor, forming Metlab-Potero and then the subsequent merger of Metlab-Potero into Metlab in December. 2009. No other heat treating company in North America has such an extensive array of heat treating furnaces, processes, and capabilities.
With furnaces ranging in size from 2 feet in diameter to 2 feet long up to 15 feet in diameter by 12 feet deep as well as up to 22 feet long, parts can be heat treated that weigh a few grams to large pieces up to 50,000 pounds.
Here are some examples of small parts that are processed in Metlab’s facility:

Processes offered include:
- Hardening and tempering
- Case hardening
- Nitriding
- Carbonitriding
- Nitrocarburizing
- Stress relieving
- Black oxide
- and more…
Recently with the addition of new vehicles and a pick-up and delivery service, Metlab has extended the company’s presence into the Maryland and Delaware markets to provide heat treating and processing services for small part needs of the manufactures and component companies in the region.
Metlab is well known for capabilities to handle very large, industrial and military parts for a variety of treatment processes. The company also works with many customers who have small parts and components for a wide variety of applications. The company is experienced in specialized packaging and shipping requirements to send the part on to the next process or to the end customer.
Call for to discuss your small part needs and specifications. Metlab is able to give you a quote and delivery schedule to meet your project deadlines.
Metlab, a Philadelphia based heat treatment company, recently heat treated custom fabricated leaf springs of an antique Alfa Romeo Sports Car, which were fabricated for a Pennsylvania based automobile restorer. The leaf springs, made from HR-5160 steel, were patterned after the original springs which were too worn to be reused during the restoration of the automobile. The replacement springs were hardened and press quenched into the shape of the spring, using a pencil drawn template made from the originals, used as a guide. Then they were tempered to a final hardness of HRC 28–32, duplicating the hardness as measured on the samples.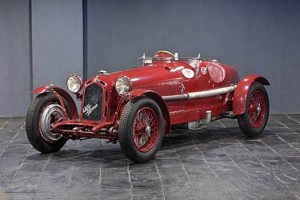
1932 Alfa Romeo 8C2300 Sports Car
The automobile, owned by a private collector, is valued in excess of $1,000,000.00. Metlab is often called upon by automobile restoration companies for heat treating reworked or remanufactured complex engine or chassis components as well as for applying black oxide to OEM automobile parts.
Another recent project included the case hardening of reground lifters from a 1962 Rolls-Royce Silver Cloud engine. The lifters has exhibited about 0.010″ wear, were reground to make them all uniform in size. The grinding however had removed the case hardening, hence the requirement for recarburizing and hardening to restore the lifters to original factory specifications for case depth and surface hardness. As measured surface hardness was HRC 62.
In addition, Metlab is often called upon to nitride O.E.M. as well as reground camshafts, crankshafts and other engine components to restore these parts to original factory specifications. Camshafts are typically manufactured from 4140 or 4340 pre-heat treated steel. This steel has a hardness of HRC 28 – 32. Nitriding results in a surface hardness of HRC 60+ and a case depth of up to 0.020″ deep, providing significant wear protection for the cam lobes and gear teeth.
In addition to hardening and surface treatment services, Metlab offers cryogenic processing on automobile engine, transmission and brake parts for improving their performance extending their useful life.
For more information contact:
Mark Podob
215-233-2600
mpodob@metlabheattreat.com.
Metlab was pleased to host the Wyndmoor, PA Fire Department at it’s factory today and present them with a meter for measuring ammonia gas in the atmosphere, as well as a cash donation.
Metlab uses ammonia in one of our heat treating processes to harden the surface of steel parts like gears, automotive crankshafts and camshafts, die casting molds and forging dies, plastic mold tools and other components. The most common use of ammonia is agricultural as a source of nitrogen for fertilizer, but it is also used in water and waste water purification systems, and industrial refrigeration systems. The detector will allow for determining the amount of this gas in the atmosphere to ensure safe levels in the environment. Without their own detector, the Fire Department, in the remote possibility that ammonia needs to be measured in any location in Wyndmoor needs to rely on the Montgomery County Hazardous Materials response team to visit the site and use their own detector. The detector is accurate enough to measure ammonia in parts per million, and is sensitive enough to measure extremely low levels of the gas.
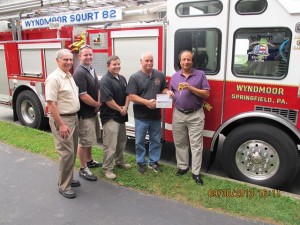
Accepting the meter and check is Fran DePaul, Fire Chief. Jim Conybear, on the far left, and Mark Podob, on the far right making the presentation are the co-owners of Metlab.
|