Metlab recently undertook a project with a major crane manufacturer to flame harden the bridge crane wheels for a large overhead multiple bridge crane system. The crane is installed at an aircraft manufacturer and is used to lift airplanes as they are being assembled. Over 1,500 wheels approximately 6 1/2″ O.D. x 2 1/2″ wide, made from 1045 steel were hardened. The requirement was a hard and uniform outside rim hardened to 425 BHN (HRC 45) and a case depth of 1/8″, minimum.
Flame hardening is a surface hardening treatment where the outside of the component is uniformly heated by direct application of a flame. Special burners combining a fuel gas (typically acetylene or) and oxygen are used to generate the flame. Temperature is monitored optically comparing the color of the heated steel to a color/temperature chart as well as using infra-red temperature sensors. When the surface of the part has been hardened to a sufficient depth, the surface is then rapidly cooled by either oil or water quenching, depending on the material being hardened.
The component is then tempered to the appropriate hardness and microstructure. The advantage of flame hardening for a part like a crane wheel is that the process hardens the outside surface only providing a deep case. This results in a highly wear resistant surface, as well as increased bending fatigue strength, while leaving a tough core which can absorb shock, and loading. And as opposed to through hardening, since only a small portion of the wheel is hardened (the surface) there is little or no distortion.
Gears, wheels, rolls and other cylindrical parts are spin flame hardened. They are placed on a motorized table, as shown in the figure, and spun while a flame impinges on the outer diameter of the wheel. For flame hardening to be effective, the component being hardened must have a carbon content of greater than 0.3 % carbon. This includes steel as well as cast iron components. Metlab has the ability to flame harden parts up to 14″ in diameter. Metlab can also flame harden rectangular pieces, like gear racks, machineways, rails, and wear plates.
Metlab has also flame and induction hardened the treads of crane sheaves, crane gears, and also rollers. In addition to these components, Metlab has carburized and hardened other crane components, most significantly hoist drums. These drums are the large cylinders that are used to take up crane wires. While some hoist drums are made from an alloy steel like and are flame hardened, it is not uncommon for the hoist drum to be made from low carbon steel like A-36 to save the cost of material and fabrication and then carburize and harden the drum. Carburizing provides abrasive wear protection to the grooves in the hoist drum, where the hardened steel wires are wound onto the drum.
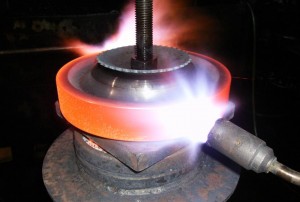
1045 Steel Bridge Crane Wheel being flame hardened. Wheel is placed on a motorized turntable and burners apply flames to uniformly heat the rim of the wheel to the appropriate hardening temperature. When the rim has been soaked through, it is rapidly quenched, and then the parts tempered resulting in the high hardness required for the application.
Metlab has over 1,500 customers and heat treats a variety of parts and materials to different specifications. The specifications which are adhered to are either customer standards or processing requirements dictated by the SAE AMS (Society of Automotive Engineers/Aerospace Material Specifications). Metlab is committed to providing quality in every step of its production processes and strictly adheres to all of the requisite standards specified by its customers.
The company has four metallurgists on staff, including not only top management, but a Quality Assurance Manager and Laboratory Manager. The QA Manager responsibilities are the monitoring, documenting and ensuring that specifications are being met and a consistent high- level of quality is achieved for every part processed. Metlab has an in-house metallurgical laboratory for testing the parts, or samples from heat treat lots for conformance to customer requirements.
Each job that comes into Metlab has some form of specification which accompanies the part or component. It might be as simple as a desired hardness range, or more complicated, incorporating case depth, tensile strength, impact properties or other mechanical property requirements. In some cases, the specifications conflict with the process or desired result, and other times they are somewhat “loose” and require clarification.
Other jobs have multiple specifications which need to be met through several processes. As an example, heat treating to AMS 2759, which is a general overview specification followed by black oxide finishing to MIL-DTL-13924. Or adherence to AMS 2750, which dictates temperature uniformity of furnaces. Metlab has on its staff several industry experts, including its Director of Operations, who is on the AMEC Committee (Aerospace Material Engineering Council). This group writes and edits the AMS specifications to provide clarification and guidance to the customers to achieve the correct results for heat treated product is achieved.
At the beginning of the process, each job is reviewed thoroughly and documented with a Shop Order Process Requirement Form. This form is issued to the shop when the order is released for production. Simultaneously, an Order Acknowledgement Form is e-mailed or faxed to the customer acknowledging receipt and acceptance of the order, and providing an estimated shop date. The Shop Order Process Requirement Form has the instructions necessary to process the job as it moves throughout the shop floor. Its focus is to provide specific information for each step in the process. A test piece also accompanies the job and is evaluated at the end of the process ensure quality, aesthetics and specification requirements.
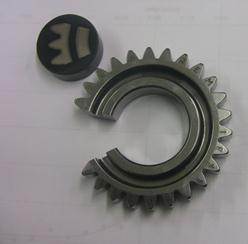
Test piece from a gear heat treating project. Note that a segment of the gear has been removed, mounted and polished so it can be evaluated for microstructure and case depth.
Each Metlab furnace is equipped with a monitoring system to check temperature, uniformity, gas flows, pressure, and other process variables. While most of the furnaces are automatically controlled, furnace operators are watching and checking as a back-up for any changes in process or possible variables that could affect the quality of the heat treat lot.
Furnace controls are calibrated quarterly as well as furnace temperature uniformity checked twice a year to ensure adherence to AMS specifications. And any thermocouples used to control or monitor temperatures are calibrated to NIST standards. Metlab furnace operators undergo rigorous training not only in the operation of furnaces and related processing equipment, but also basic metallurgical principles so that they have insight into the overall heat treatment procedures to treat different materials.
After the job has gone through the production process, a part or multiple parts are tested to check that the job meets specifications and quality level. These pieces may be checked for conformance to hardness or other mechanical properties. And parts are inspected visually as well. Hardness testers, microscopes and dimensional measuring equipment are all calibrated according to a fixed schedule.
Once a part clears the production process inspection, it goes to the Quality Control manager for final review. Upon approval, a Quality Certification is developed and shipped with the parts to the customer.
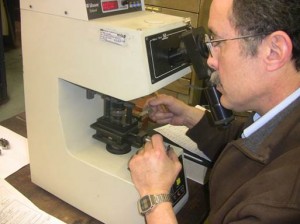
Laboratory Manager testing microhardness on a cut, mounted and polished sample to ensure that case depth specification is met.
High-quality is a constant focus and core competency throughout the company and an emphasis on quality is part of the company Mission Statement. Metlab furnace operators undergo rigorous training not only in the operation of furnaces and related processing equipment, but also basic metallurgical principles so that they have insight into the overall heat treatment procedures to treat different materials.
And on-going safety training of all employees, conducted by recognized and accredited industry experts for all aspects of shop operations is key as well. Metlab processes parts for critical applications and is able to achieve consistent quality levels. The QC organization is well versed in working with on-site auditors for special jobs, crucial parts and components. It is not unusual to see a Government Source Inspector or outside customer auditor at Metlab working to verify that the requirements of heat treated components has been met before parts are allowed to ship.
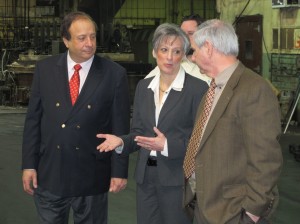
Mark Podob (left) and Jim Conybear (right) owners of Metlab, Philadelphia, PA, welcomed the Honorable Allyson Schwartz, Congresswoman to Metlab on Thursday, April 4, 2013.
The Congresswoman, Representative for the 13th District in Pennsylvania, toured the heat treat plant looking at the two largest pit furnaces in North America as well as such diverse projects as the manufacture of wire supports for the arresting cable mechanism on aircraft carriers, carburizing and hardening crawler shafts for steam shovels, and gears being nitrided for Navy destroyers.
Also noted was the company’s black oxide line used for finishing fasteners, machined parts and other components. Discussions focused on issues facing small businesses, Metlab concerns for the future of manufacturing in Southeastern Pennsylvania and ways for attracting and retaining a skilled workforce.
In anticipation of receiving several large gears and bearing races for carburizing and nitriding, Metlab has completed the upgrade of both of its large pit furnaces. The upgrades enhance the company’s capability to process parts up to 14 feet in diameter by 12 feet long and up to 50,000 pounds. The equipment improvements included refurbishment of nickel base alloy retorts to maintain the appropriate furnace atmosphere, new insulation, and upgrades to burners, burner controls and other instrumentation. Now two furnaces, each of similar size and each with 4 million BTU/hour natural gas heating capability sit side-by-side, adjacent to two quench tanks for oil or water medium quench. Twin overhead cranes, with a combined lifting capability of 25 tons are positioned over the furnaces to load and unload components. Temperature uniformity surveys of both furnaces performed in accordance with AMS 2750D showed that the workzones were +/- 11.5°F at 1750°F, well within the specification requirements of +/- 25°F.
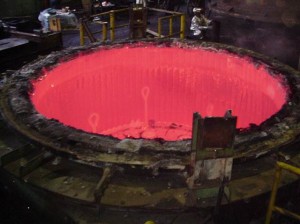
After commissioning of the upgraded furnaces, Metlab commenced carburizing two large 12,000 pound gears, 11 feet in diameter by 7 1/2 inches thick. The gears were carburized to a case depth in excess of 0.250″. The temperature uniformity of the furnace, coupled with special fixturing for supporting the gears during carburizing and hardening, resulted in a heat treated product with minimal distortion and taper. An upcoming contract for nitriding six large main propulsion ship drive gears, each 10′ in diameter by 8′ tall, weighing in excess of 20,000 pounds each, will be run in the furnaces. Company spokesmen indicated that the furnaces would see extensive use for carburizing, nitriding and hardening large gearing as well as heat-treating large carburized bearings destined for use in wind energy turbines.
With over 30 furnaces on-site, the largest 15 feet in diameter, and the longest 24 feet deep, and 40 employees working on three shifts, Metlab, located in Philadelphia serves an international marketplace with an array of comprehensive thermal processes. These include carburizing, nitriding, hardening, annealing, stress relieving, black oxide and other services.
For more information, contact Mark Podob, Vice President, Metlab, 1000 E. Mermaid Lane, Wyndmoor, PA 19038, 215-233-2600, mpodob@metlabheattreat.com.
Christini Technologies is a Philadelphia-based, manufacturer of custom all-wheel drive motorcycles. Known for manufacturing custom motorcycles for competition racing, Christini was recently awarded a contract to supply the Army with 450 tactical scout bikes to be used in worldwide operations.
Integral to the construction of the motorcycle and the performance of the bike is a special welded aluminum alloy frame. Because the frames are of a welded construction, they must be heat treated to restore the mechanical properties to eliminate the soft zone adjacent to the weld. It is critical for the application that the mechanical properties of the welded aluminum frame are restored to the original requirements so the frames do not prematurely fail during use. Metlab is the vendor of choice for the heat treating.
Steve Christini, owner of Christini Motorcycles explains, “During the manufacturing process of the motorcycle frame, you cut the head tube off then weld the frame. This changes the integrity of the metal. Heat treating brings it back to the correct specifications. Then a finish blast is used for aesthetics. We use Metlab because of the way they do the entire heat treating process. The parts are not contaminated and their process is a very clean process. This enhances the strength and integrity of frame.”
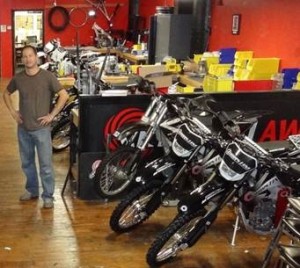
Steve Christini owner of Christini Motorcycles
The material used in the frames is 6061 Aluminum. It is specified due to its strength, heat treatability, comparatively easy machining and weldability. Prior to heat treatment, the frames are cleaned to be free of any grease, oil or other contamination that may affect the parts. The frames are then heat treated to the T-6 condition, which consists of solution treating, or heating the parts to 985°F, holding for one hour at temperature and then immediately water quenching. Then the frames are age hardened at 350°F for 8 hours.
We have a load thermocouple that indicates when the part is up to the appropriate temperature. The soak time is dictated by the maximum section thickness.
After heat treatment, the parts are checked for hardness and conductivity to ensure that they meet the mechanical properties for properly heat treated frames. This process uses a calibrated micro-hardness tester and is carried out by trained quality control personnel.
Furnace temperature uniformity is the key to ensuring uniform mechanical properties, and the furnaces used for processing the frames are uniform within +/- 15°F in the complete work zone.
During the inspection process we make sure the mechanical properties, primarily hardness, fall into the process requirement range:
Reference MIL-H-6088, AMS 2770
Solution Treat Quenched Condition W
Age Harden- T6
80 BHN500 – min; 42 HRB; 78 HR15T, 40-50 Conductivity
Solution Treat (Condition W as quenched, T4-natural age at room temperature)
Age Harden – T6 Condition (Artificially Age Harden)
A visual inspection is conducted to determine if there are any types of defects especially around the integrity of the welds.
It is important to position the frames in the furnace so they do not distort during heat treating and also water quenching. While not the case with this particular application, Metlab heat treats certain parts for some customers who weld braces in place to keep the parts from moving. Also, for some customers where distortion is especially critical, parts are straightened before age hardening.
There is special engineering involved in the heat treat relating to the fixturing to both hold the parts and minimize distortion, as well as minimize transfer time. The parts are placed on special fixtures to keep them upright so not distortion from sagging. No special materials are needed for processing, just special equipment.
Metlab often turn parts around for Christini Motorcycles within a few days after receipt, and have given the company routine Friday to Monday service. Currently over 75 frames have been heat treated and processed by Metlab in 2011.
Mark Podob
Metlab Heat Treating
The use of a press quench for hardening products allows for tight dimensional control of the heat treated part. The benefit is reduced post-heat treatment grinding time, resulting in significant cost savings. Parts press quenched are typically bearing races or gears. The bearing races are made from either 52100 steel or from carburizing grades of steel which have first been carburized to the appropriate case depth required for the product. Gears which are press quenched are also first carburized and slow cooled.
For press quenching parts at Metlab, parts are placed in an atmosphere controlled Rotary Hearth Furnace. The furnace atmosphere (which is endo-based) is adjusted to match the carbon content in the part to avoid carburizing or decarburization. The furnace is able to accommodate parts up to about 18 inches in diameter. The furnace hearth, which is about 48″ in diameter, accommodates up to 8 pieces at a time. The parts are loaded sequentially, one at a time, with the furnace indexing an eighth of a turn between loading. Once the furnace is fully loaded, the number 8 piece is at the door, fully soaked out at the hardening temperature (1550°F) and is ready for quenching. The part is removed from the furnace by the operator using a robotic arm.
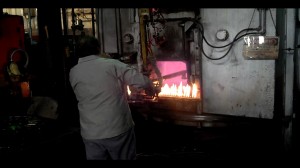
Operator picking up a bearing race which is at 1550°F,
from the Rotary Hearth Furnace using a robotically
controlled transfer mechanism.
The heated part is placed in the press which consists of two conical dies; an upper and a lower die. The part is placed on the bottom die, and then, the entire bottom die moved into the quench area. A tapered top die comes down to meet the part, centering the part on the die and locking it into place. The part is then quenched using high velocity oil which flows through nozzles positioned 360° around the O.D. of the part, allowing the quenched part to take a set.
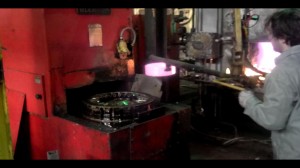
Part is moved to the press quench
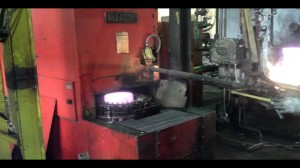
Part is placed on the lower die
The use of press quenching can allow for quenched and tempered product which is round and flat < 0.005″, providing for significant reductions in machining times over parts which are free quenched. Cycle times for quenching parts range from 2 ½ to 10 minutes depending the size of the part allowing for relatively high production rates.
Mark Podob
Metlab Heat Treating
Metlab has heat treated a series of aluminum trusses used to tether aerostat balloons. The trusses, fabricated from 6061 Aluminum were placed in a rigid fixture with a 13′ x 6′ wide foot-print, 12′ tall, developed to hold three trusses per heat treat cycle. Each truss was over 12′ long. Parts were hardened by solution treating at 985°F, held for one hour, and then water quenched. They were then hand straightened over the complete span, and age hardened to the T-6 condition (350°F/10 hours). The pit furnace utilized for the thermal treatment measures 15′ in diameter by 12′ deep, and has a retort to allow for processing parts under inert atmospheres. The heat treated trusses comprise a section of the entire mooring assembly, which is over 24′ long, used to anchor the balloons.
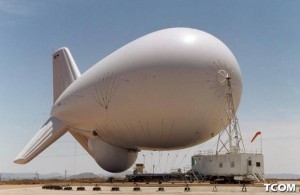
Metlab, based inWyndmoor,PA is a specialized commercial heat-treating facility serving a domestic and international customer base. The company’s broad range of precision thermal processing capabilities include normalizing, hardening and tempering atmosphere annealing, stress relieving, age hardening, carburizing, nitriding, and boronizing, particularly very large parts to very deep case depths. The company also provides metallurgical consulting services. Parts processed range from those a few ounces in weight to pieces up to15 feet in diameter by 24 feet long. With a fleet of vans and trucks, Metlab offers a pick-up and delivery service to customers in the region.
Metlab provides thermal processes in accordance with most military specifications, and is an approved supplier of heat-treating, black oxide, and coating services to many of the major manufacturers and Fortune 500 companies.
Metlab Heat Treating was founded just outside of Philadelphia in 1928, Metlab has innovation in its DNA. Originally a manufacturer of aircraft components, it began heat treating as part of the process, developing the “drop bottom” or “gantry” furnace along the way in order to minimize distortion in the delicate aluminum parts it was making. It continued developing its expertise in deep-case carburizing over the years, building huge furnaces to treat large components such as bearings and gears for the mining, industrial, and energy markets, among others, as well as for military applications. It was this history, along with its expansive capabilities, that drew the attention of two heat-treating professionals in 1998.

“One of the most attractive things about the company was the facility itself,” according to Mark Podob, vice president of marketing and sales and co-owner along with Jim Conybear, director of operations. “We have a pit furnace that’s 15 feet in diameter and 13 feet deep that we used to nitride the main propulsion gears for the U.S. Navy’s Seawolf class of nuclear submarines, for example. It can accommodate a 43,000-pound gear, along with other very large components, and it can provide a variety of treatments.”
Among its long list or services are metal hardening, quenching, and tempering, induction/flame hardening, vacuum heat treating, annealing and protective atmosphere normalizing, carburizing, carbonitriding, nitrocarburizing, boriding/boronzing, cryogenic treatment, and heat treat stress relieving.
The company also provides metallurgical consulting—supported by its fully equipped laboratory—and the fabrication of special parts. It can heat treat parts from one pound to 25 tons, and having so many tools in its belt allows Metlab to address its customers most-complex challenges.
“We view ourselves as consultative heat treaters,” Conybear says. “For instance, a customer came to us about 10 years ago who was having a problem with the rails inhis material handling system. He was using carbon steel, which was only lasting a year,and we suggested that he make them out of tool steel because of its excellent wear characteristics. He ended up asking us to design and manufacture the whole system, which we did, turning a $20,000 order into one worth around $300,000. But he hasn’t had to replace those rails or even grind them in more than a decade now.” Podob agrees, recalling another project involving a large fabricated gear used in the rolling mill of a steel plant. The manufacturer needed help controlling distortion, so Metlab joined a multi-company team in addressing the problem. “It took us about a year to arrive at our lowest-possible distortion,” he explains, “and not only did it require refining the design of the gear, we also had to change the manufacturing process and sequence, and even develop special fixturing in the heat treatment cycle. This gear had a three-foot face width, a case depth in excess of a quarter of an inch, and when we were done it was round within 30 thousandths. The only downside was that they only need one of those every 10 years or so.”
More capabilities were added in 2001 with the acquisition of J.V. Potero, Inc., which specialized in the protective atmosphere heat treating of small to medium size batches, induction hardening, and black oxide finishing of steel parts. The acquisition was part of a careful strategy the two partners have developed. “When Jim and I bought the company, it was primarily focused on these extremely challenging ‘one-off’ projects, and even though we’re both drawn to that type of work we realized that we also need to make payroll,” Podob says with a laugh. “So in recent years we’ve really worked hard to pull in some ongoing contract work, as well.”
Still, the two men thrive on identifying solutions to the problems its customers encounter. “We’re basically a job shop going from project to project,” Conybear says, “so you never know what you’ll find when you step out into the productionarea. What you’ll see one week will be completely replaced by an entirely different range of products next week. And while it’s a challenge to schedule that type of work, we spend a lot of time writing process specifications and making sure the job is done correctly from start to finish. We really pride ourselves on taking that type of approach, and I think it’s something our customers appreciate as well.”
Recently, Philadelphia Gear, A Brand of Timken Gears & Services Incorporated was awarded a contract by the U.S. Department of Defense for the supply of main reduction gears for the new Arleigh Burke Class Guided Missile Destroyers. Philadelphia Gear has been a long standing Metlab customer for over 50 years. Metlab will be helping with the heat treating of these gears.
The gears will come to Metlab’s facility one at a time in specially built wooden crates. Each gear is ~ 112″ in diameter by 86″ tall and weighs about 20,000 pounds. There will be a total of six gears initially required for the destroyer project. The gears are a fabricated, welded construction, with the gear teeth made from a special alloy developed specifically for nitriding. Upon receipt, the gears will be cleaned and then placed in one of Metlab’s two pit furnaces for nitriding. Six (6) thermocouples will be positioned on the gears to make sure that strict temperature uniformity is met. The furnaces have work zones that measure 15′ in diameter by 12′ deep, and 12′ in diameter by 10′ deep respectively. It is expected that the parts will be in the furnace for at least a week at temperature. Upon completion of the nitriding process the gears will then be sandblasted clean to remove maskant, and shipped back to the customer.
During the course of the project, government inspectors will be on-site, monitoring the various stages of the project to ensure that processes and specifications are met to the high standards for this application. Metlab is familiar with working with these inspectors and providing them with the access and information necessary to ensure a smooth and compliant processing job. These gears are also on a time-sensitive schedule with tight deadlines.
Main Drive Gear for a nuclear submarine, similar to those referenced above, nitrided to a 0.040″ case depth. Gear measures 12′ in diameter by 12′ tall and weighs approximately 24,000 pounds. Gear hub, bore and web faces have been masked to prevent Nitriding to allow for post heat treatment machining.
Metlab has accommodated many government and military projects including flight critical components like wire supports for aircraft carriers for the Navy. The company has the experience, facilities and resources to comply with all specifications and regulations for these projects and more.
Mark Podob
Vice President of Sales
Metlab Heat Treat
Metlab has shipped Machine Ways used to guide the track wheels of a precision industrial aluminum machine used for cutting wing segments and fuselage frames for commercial and military aircraft. Metlab chose A-2 tool steel as a replacement for the original cold fused flame hardened bi-metal steel design, which failed at the junction of the two dissimilar metals. The selection of through hardened A2 eliminates the need for complete replacement of the machine ways due to wear in service.

The Machine Way consists of eleven 12 foot long bars connected end to end, 2″ thick by 6″ wide, match ground to ± 0.003″ in length, ± 0.0005″ in thickness, with a maximum joint gap < 0.004″ between adjacent bars. The overall Machine Way is over 130′ long when installed.
Metlab was chosen to manage the entire project which involved partnering with the material supplier and grinding source to solve the unique problems presented by the Machine Way design. A2 tool steel needed to be obtained in the special length and size. Domestic material was purchased from the one source in Illinois which allowed for timely delivery.
The bars were heat treated vertically in Metlab’s unique 48″ diameter by 16′ long vertical pit furnaces under a protective atmosphere to ensure no decarburization or oxidation. The individual bars were straightened to less than 0.050″ in special fixturing provided by Metlab. Precision drilled and tapped locating holes (over 24 on the length of each bar) needed to be placed in the bars before heat treating. The use of low expansion A2 selected by Metlab allowed for predictable compensation for movement during heat treatment. The finished bars were then precision ground.
Metlab’s expertise in overall project management, background in material selection, and experience with large shape heat treatment produced a dramatic improvement in the component without a sacrifice in the machine design.
Mark Podob
Vice President of Sales
Metlab Heat Treat
|