Recently Industrial Heating Magazine featured Metlab as part of a company profile as a member of the Metal Treating Institute:
Metlab isn’t your typical commercial heat treater. Founded in 1928 as a manufacturer of aluminum spars for biplanes, the company is credited with the patent for the first drop-bottom gantry furnace.
But today, the Wyndmoor, Pa.-based company is known for its huge pit furnaces and its ability to heat treat parts weighing anywhere from a few ounces to 50,000 pounds. In fact, Metlab has more than 30 furnaces on-site – including pit furnaces as big as 15 feet x 12 feet deep, which are believed to be the largest in North America.
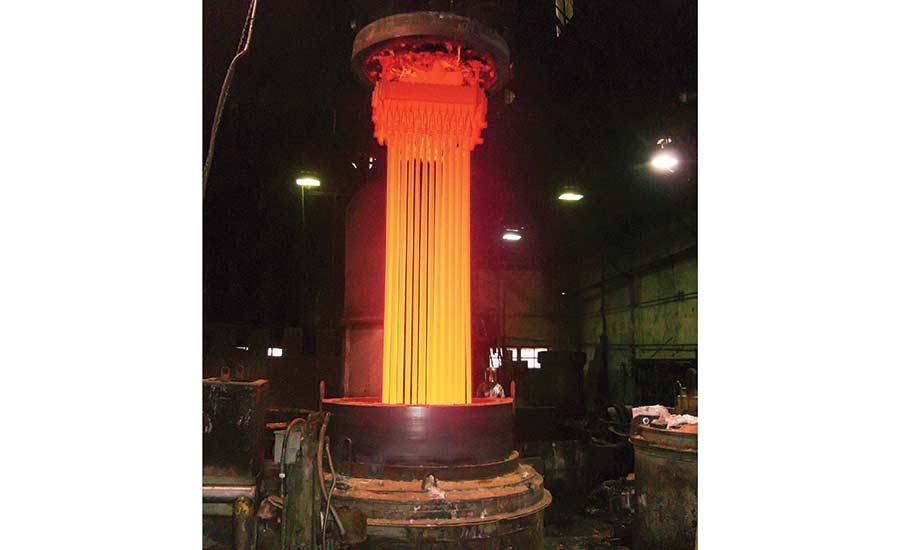
Load of modified H-11 steel rods, 2 feet in diameter x 16 feet long, being prepared for air quenching.
The company also has vertical pit furnaces measuring 4 feet in outside diameter x 16 feet deep with the ability to extend to 18 feet deep for heat treating long, slender parts used in oil drilling, mill pinion shafts, bar stock and tubing. A pit nitriding furnace and a car-bottom tempering furnace (6 feet x 9 feet x 16 feet) complement the large-parts department, and the company has several integral-quench batch furnaces and support tempering equipment for heat treating small parts.
Metlab acquired the John V. Potero Company in 2001, allowing it to process small parts and provide a wide range of heat-treatment services. These include case hardening, nitriding, protective atmosphere annealing, hardening, quenching, tempering, stress relieving, solution annealing and age hardening. What’s more, the recent investment in vacuum furnaces has further expanded the company’s offerings into bright hardening of tool steels and stainless steel.
Deep-case carburizing and hardening, as well as nitriding of large and small gears and shafts, are core competencies of Metlab. The ability to heat treat these parts to precise and accurate case depths and hardness while maintaining geometric integrity makes the company unique in the field of commercial heat treatment. What really sets the company apart from its competition, however, is its ability to process parts in large, atmosphere-controlled equipment specifically designed for processing gears, pinion shafts, bearing races and other large industrial components.
This longtime MTI member offers more than thermal processes. With three full-time metallurgists on staff and an in-house metallurgical laboratory, Metlab has the ability to analyze microstructure and case depth to ensure all parts are processed accurately and on time. The company also offers black oxide finishing, failure analysis and metallurgical consulting.
As for recent developments, a recirculating water system funded in part by a grant from the Department of energy coupled with rebuilds of the two large pit furnaces has made Metlab more competitive from a cost-savings and water-recycling standpoint.
As for the future, Metlab intends on acquiring new equipment and adding new processes to complement its core offerings. Recent projects involving the heat treatment of nose cone and rocket exhaust gas nozzles as well as long, slender down-hole tooling indicate the need for more capacity to process large parts. In addition, capacity to nitride gears, axles, shafts, and large industrial valves calls for equipment upgrades.