Black oxide, or blackening or bluing, is a chemical conversion coating that provides corrosion resistance and a decorative black finish to metal surfaces. It is commonly used on architectural metal products to enhance their appearance and protect them from rust and corrosion.
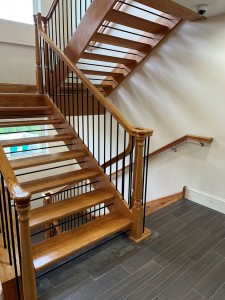
Staircase railings treated with black oxide.
When considering black oxide treatment for metal surfaces, it’s essential to consider various technical factors to ensure the desired results. Metlab has extensive experience and capabilities to help create the best possible treatment process and can accommodate parts up to 40” long for black oxide treatment.
Consultation and Testing:
The best way to start your black oxide project is to consult with Metlab. The consultation will ensure that you can achieve consistent results for large architectural projects, especially where variability in color or finish can be undesirable. Tests on sample pieces can be performed to optimize the black oxide process to control the variability and consistency for your specific project.
Cost and Maintenance:
The experienced treatment specialists at Metlab will help you evaluate the cost of black oxide treatment and the long-term maintenance requirements. This process will help you consider whether it is cost-effective and practical for your project.
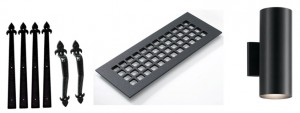
Examples of architectural products with black oxide treatment include door hardware, grates, lighting, and more.
Technical Considerations:
- Metal Type and Composition:
- The type of metal you’re treating will affect the black oxide process. Different metals may require specific solutions or pretreatment steps to achieve the desired finish.
- Surface Preparation:
- Proper surface preparation is critical. Metlab ensures the metal surface is thoroughly cleaned and free from contaminants like rust, oils, and dirt.
- Black Oxide Solution:
- Metlab formulates the appropriate black oxide solution based on the metal type and desired finish.
Quality Control:
Metlab technicians regularly inspect the parts during the process to ensure they meet the desired color, quality, and thickness of the black oxide layer.
Balancing the technical considerations with your architectural metal project’s specific requirements and aesthetic goals is crucial. Seek guidance from Metlab, which is experienced in metal finishing and black oxide treatment, to ensure the best results for your unique application.
Posted in Black Oxide
|
Tagged Black Oxide
|
Metlab has recently added a second production line to bolster its black oxide capabilities, providing the company with an additional 50% boost in capacity.
The new line consists of nine (9) individual tanks, a caustic cleaning tank, an acid tank, two rinse tanks, a black oxide tank for low carbon and alloy steel parts, a tank for stainless steel parts, another rinse tank, and a hot dip dry-to-the touch oil tank. The tanks are 2′ x 3′ x 3′ deep with an estimated capacity range of 200 – 400 pounds per hour based on the configuration of the processed parts.
Black oxide treatment production line.
Black oxide is an effective surface treatment that enhances the corrosion resistance, wear resistance, and aesthetics of components used in various industries. By significantly expanding its black oxide capabilities, Metlab will be better able to serve its clients by increasing its work volume and processing an even more diverse array of parts.
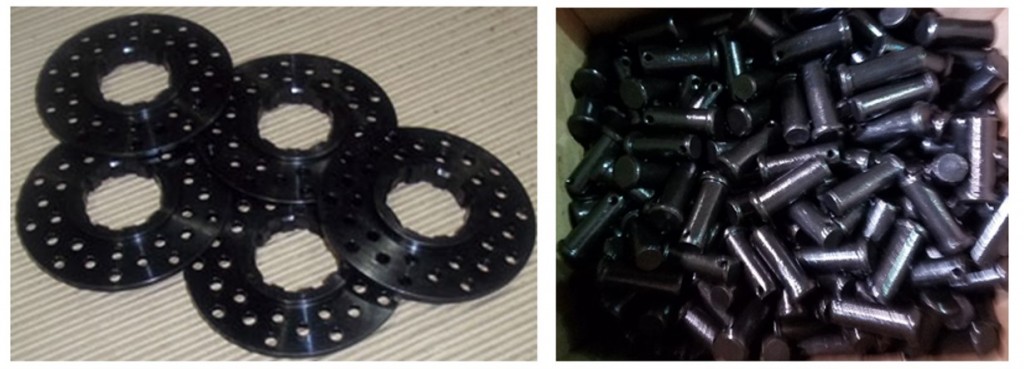
Metlab provides black oxide treatment on various parts, from gears, blades, and bushings to pins, connectors, and much more.
“Our recent addition of a second production line marks a significant milestone for Metlab, allowing us to further enhance our black oxide capabilities and expand our capacity to meet the growing demands of our customers,” said Mark Podob, President of Metlab. “We are proud to continue providing cutting-edge heat-treating services for a wide range of parts while maintaining our unwavering commitment to quality and customer satisfaction.”
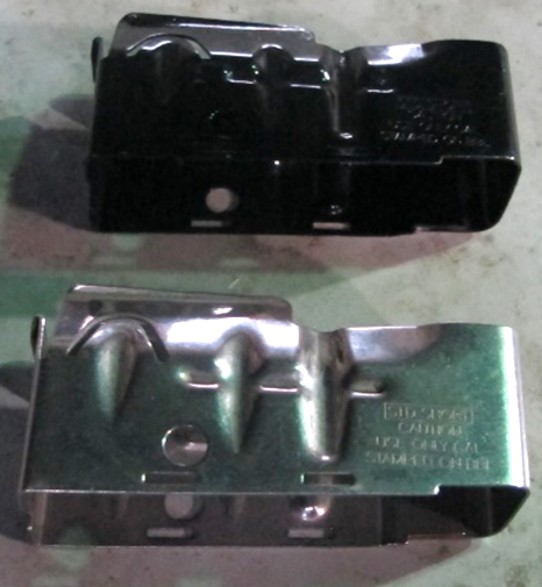
Before (bottom) and after (top) black oxide treatment to shotgun shell magazines. Black oxide perfectly replicates the surface finish while protecting the surface from rust and oxidation.
Black Oxide processing provides a highly cost-effective form of protection and adds to the component’s resistance to corrosion. The process adds no dimension change to the component dimensions and improves the visual quality while offering lubricity. In addition, thin parts can withstand bending, stretching, and handling. Black oxide coats all surfaces of a component.
Typical applications are fasteners, machined components, stamped components, guns and ammunition, tools and dies, power tool components, automotive parts, exercise equipment (weights), electronic hardware, and architectural finishing.
Recognized for its advanced facilities and extensive expertise, Metlab has built a reputation for providing heat-treating services that cater to a diverse spectrum of parts, from the smallest components weighing just one pound to massive parts weighing up to 25 tons.
Metlab continues to position itself as a reliable partner for both domestic and international manufacturers. As an industry leader, Metlab is prepared to handle the evolving needs of its customers, providing superb-quality products and the highest standards of workmanship.
Posted in Black Oxide
|
Tagged Black Oxide
|
Metlab was recently featured in the Heat Treat podcast discussing” ultra large gears” and very deep carburizing. Host Carlo Torres interviews Mark Podob, Metlab’s company owner and president, during the podcast. They review Mark’s professional background and how Metlab originated. The company was started in 1928 and specialized in heat treating large components such as gears and bearings. Mark and his partner bought the company and expanded it. The company has grown from 18 employees to 40 people.
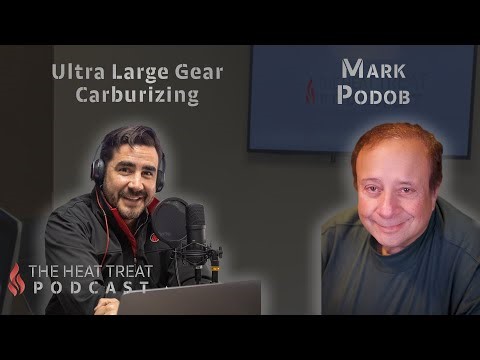
The Heat Treat Podcast #49 features Mark Podob,
President and Owner of Metlab Heat Treating
Click to watch: https://youtu.be/k7JiXwaip-U
Podcast host Carlos Torres encourages the audience to go to the Metlab website. “The pictures of huge gears and pinions in the heat treating process are amazing.”
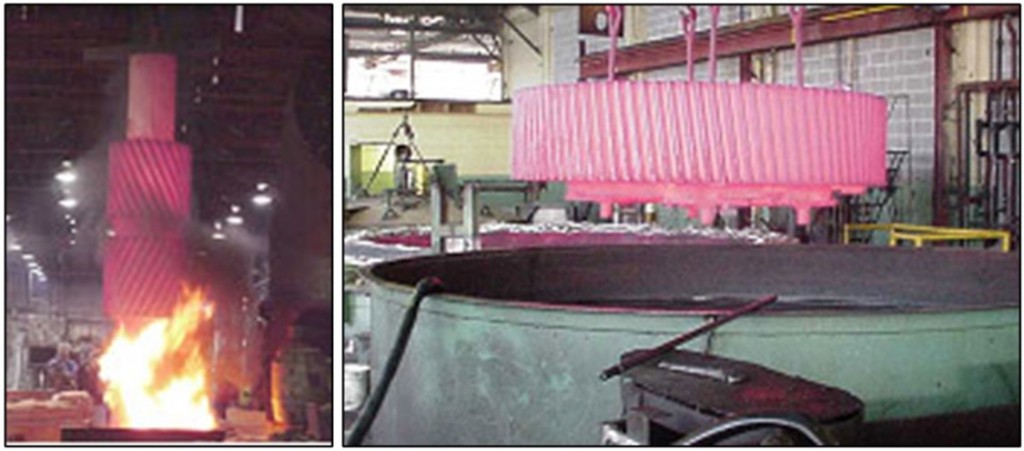
www.metlabheatreat.com
The company installed a large furnace in the 1980s because they had landed a contract from a company making transmissions for the Sea Wolf submarine. These giant gears weighed 20,000 pounds and were the main propulsion drive systems for the submarine. The gears were about 12 feet in diameter by 12 feet tall and were being nitrated. Over time Metlab nitrated up to 24 of these gears for the submarines.
Metlab’s largest furnace is 15 feet in diameter by 12 feet tall and designed to heat treat large gears. Podob explains, “We ensure they sit in the furnace entirely flat to minimize the distortion. For example, we take a 45,000-pound gear, put it in the furnace for a week, quench it, temper it, remove it, and measure it. The quench tank associated with the furnace is about the same size and holds about 30,000 gallons of oil.
The podcast also covers more carburizing examples and Metlab’s wide range of heat treating services and capabilities.
Watch other episodes of The Heat Treat Podcast and subscribe to the channel:
https://www.youtube.com/@theheattreatpodcast6158
Metlab Heat Treating continues to encourage and support educational institutions with the development of new motorsport vehicles. Rowan University, located in Glassboro, NJ, has a team of engineering students who design, build, and race these cars each year. Metlab provides free heat treating consulting and services to support the program.
Brian Deady, Sponsorship Chair for Rowan SAE, explains, “We have two new cars in production in which Metlab will be featured, one is nearing completion, and the other is still in the design phase. We’ve been representing the Metlab brand at all meetings and events throughout 2022 and will continue in 2023. We are looking forward to a big event in Canada that will give the Metlab brand exposure in a completely different country.”
The current lineup of cars in front of Rowan University’s engineering building.
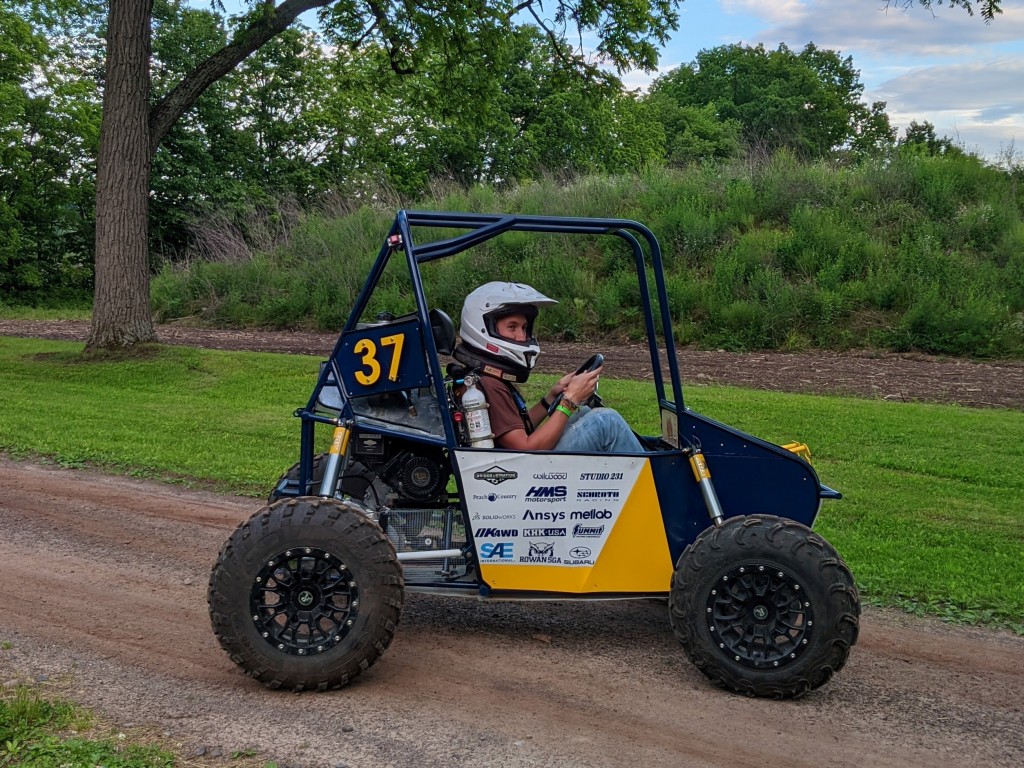
Our first four-wheel drive “Corona Car” at its competition in
Rochester, NY, in June 2022.
A rendering of the currently resigned car that will be built during the spring semester.
This semester, the team developing a new car will have gears that require hardening and a new welded frame that needs stress relieving, both to be done at no charge by Metlab.
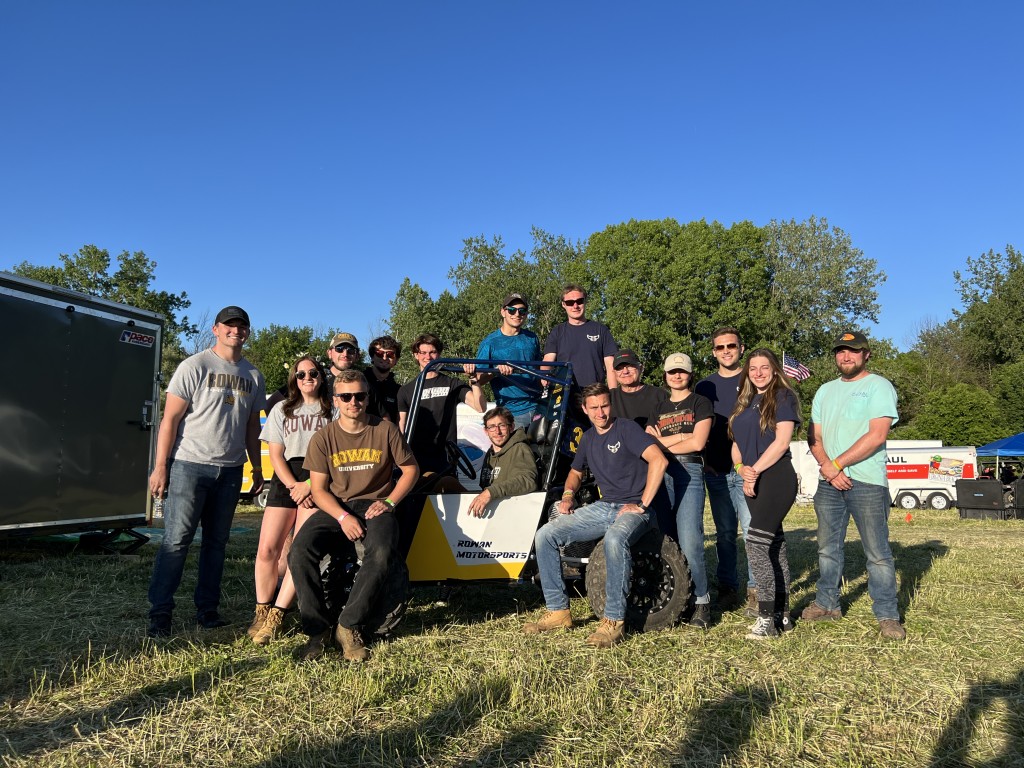
The entire Rowan Motorsports team is posing with the new four-wheel drive car.
“I just want to thank Metlab for all you have done to help Rowan Motorsports, and we look forward to continuing this partnership.” Brian Deady
Metlab company owner and president Mark Podob states, “There are two things that I am incredibly proud of as the owner of Metlab. The first is the support of Rowan University by providing not only in the form of technical advice on how to heat treat your gears, pinion shafts, and structures but also the treatment of these parts at no charge as we give back to the educational community with our services. Metlab is committed to assisting with your programs at no cost to ensure you stay competitive. The second is the shirts you provided with the Metlab logo on the back that shows we participate in the program. We wear these shirts with pride.”
Longtime Metlab employee Robert J. (Bob) Swanlund of Philadelphia passed away suddenly at his residence last week. Bob was the beloved husband of Sharon, married for over 30 wonderful years. He was the loving father of Anthony and Brianna. He will be sadly missed by his grandchildren, Alexander, Autumn, and Aiden, and his brother Arthur, and all his coworkers at Metlab, where he was a foreman.
Bob came to Metlab when the company acquired the John V. Potero Company in 2002. All told, he worked in heat treating for over 35 years. He was skilled in all phases of the small parts heat treating, particularly operating Metlab’s Sunbeam Case Master’s and Surface Combustion Integral Oil Quench furnaces, and responsible for flame and induction hardening and straightening.
Bob was more than a manager at Metlab – he was a metallurgist and understood the interaction of heat treating and material properties, often modifying recipes and heat treatment cycles to ensure customer parts met or exceeded specifications while making sure shipments were always on time.
Bob was a family man, enjoying time with his wife, daughter, and his grandchildren. He enjoyed riding his motorcycle and, unfortunately, was banged up badly several years ago, swerving to avoid hitting a cat and hitting a parked car instead. When he wasn’t spending time with his family, he loved to play pool and watch western movies. No question – Bob was a “manly man” and will be missed by his friends, family, and coworkers.
Metlab provides many services and solutions for the automotive industry. Occasionally, customers will contact Metlab with heat treating projects for their personal sports cars. Additionally, professional automobile restorers utilize these services on classic cars.
The owner of a late model Porsche 911 contacted Metlab to provide black nitriding for a set of rocker arms.
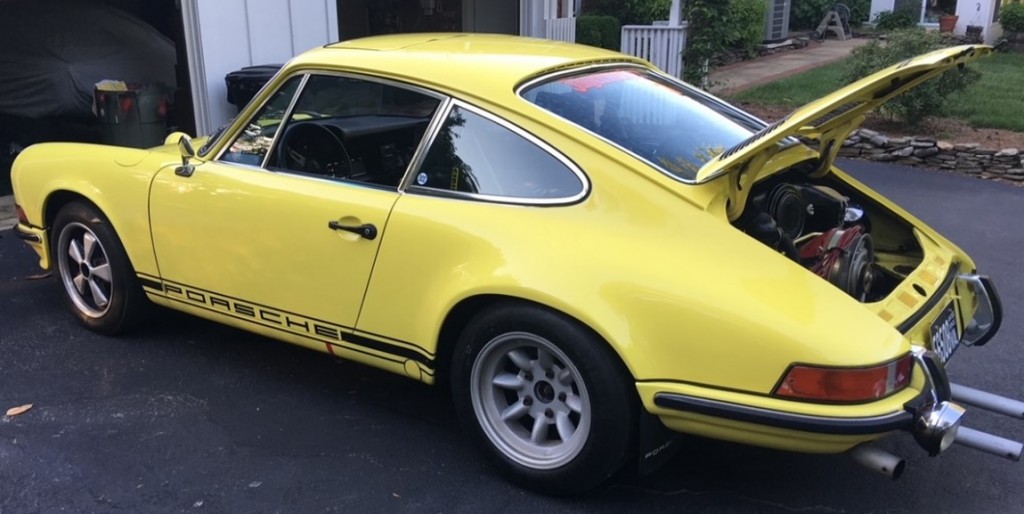
A Metlab customer’s Porsche 911 with a twin-plug 2.8 engine contracted black nitriding services for a set of rocker arms.
Black nitride is an alternate term for ferritic nitrocarburizing, a hard, corrosion-resistant surface treatment that diffuses carbon and nitrogen into the surface of the treated parts, making them very hard while retaining core strength and ductility. These specific characteristics of the process make it useful for many automobile parts.
The black nitriding process improves fatigue strength, provides exceptional lubricity, and a low coefficient of friction. The process will hold dimensional requirements with little or no distortion and provides improved wear and corrosion resistance. The result is a hardness of 52-58 HRC with a matte black color. Black nitriding also meets many mil specs as well as AMS 2753 specifications.
Contact Metlab for heat treating and black oxide treatment of parts as small as one pound and as large as 25 Tons! Metlab offers customers the broadest available heat treating, surface treatment, and size capability with a unique and extensive equipment base.
Posted in Nitriding
|
Tagged Nitriding
|
Many universities have engineering programs which include SAE International’s Collegiate Design Series competitions. These competitions afford students the opportunity to design, build and test the performance of a real vehicle and then to compete with other students around the globe in competitions. Metlab has a long history of helping academic automotive programs providing heat treat services of different automobile parts at no cost to the students or schools. The 2021 racing season for the Georgia Tech Off-Road racing team included Metlab’s heat treating services contributing to the latest vehicle build.
In an interview with Wasiq Kabir, Team Leader, he revealed that for the first time in 20 years of competing, the team developed their first-ever 4-wheel-drive vehicle. The process required a heavy emphasis on design, fabrication, and validation and an extensive amount of effort from each team member.
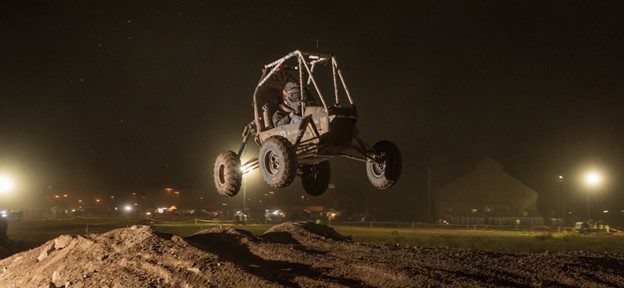
The new Georgia Tech Off-Road Racer flying high
over obstacles on the track.
Wasiq explains, “Metlab heat-treated all of our gears and shafts for the vehicle’s transfer case that is part of the drivetrain system to power the car’s front and rear wheels. They used their nitriding process. Additionally, Metlab heat-treated our front and rear half-shafts as well as our driveshafts, and they used nitro-carburizing to get high surface hardness without deforming the components.”
It took approximately two weeks to receive the parts from Metlab. “We asked them to hurry the job, and they came through for sure,” Wasiq exclaims. “It’s critical to heat treat these parts because they are all susceptible to surface wear. These parts rotate at high speed, meaning they see high-frequency loading, and one failure mode could be surface wear between any two mating contact surfaces. For example, the gears are spinning at high speed, and the teeth’ faces are rubbing against each other as they mesh. Having a high surface hardness is important for long-lasting gear teeth.”
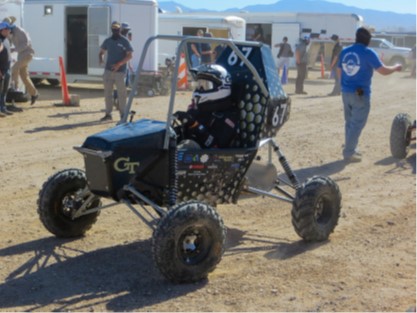
High frequency loaded parts were heat-treated
to achieve a high surface hardness to reduce surface wear.
The gears and shafts that were heat-treated by Metlab were assembled into the transfer case and 4WD system. These parts never failed throughout the Endurance races and earned the team the awards of Best 4WD Vehicle and 2nd place in the Endurance race at the official Baja SAE Louisville competition. Wasiq exclaims, “Our best performance in decades wouldn’t have been possible without Metlab’s support, so thank you!”
For information on utilizing Metlab’s no charge assistance for an SAE Automotive program, contact Mark Podob, President of Metlab, mpodobmetlabheattreat.com, 215-233-2600 Ext. 232.
Cryogenic processing is a special type of heat-treating process that involves cooling heat-treated steels and other metals to temperatures lower than -300°F. The deep chilling of heat-treated parts allows the metal molecules to be brought to “cryogenic stillness” to improve wear characteristics. When heat-treated steels are cooled to extremely cold temperatures, retained austenite is transformed to martensite, completing the heat treatment process. Retained austenite is brittle, and if not transformed to martensite, can cause chipping or cracking. As a worse case, retained austenite can act as nucleation sites for metal fatigue. Many heat treatment specifications, specifically for critical applications such as carburized gears or bearings, require deep-freezing the parts and a subsequent tempering operation to reduce or eliminate retained austenite and transform it to tempered martensite.
Cryogenic processing is performed by slowly cooling parts in a controlled bath of liquid nitrogen or a freezer, holding the parts until equilibrium is reached with the liquid’s temperature. Nitrogen is a liquid at -320℉. Cryogenically processed parts are generally held for one hour per inch of thickness. They are then gently heated to room temperature. For carburized and hardened steels and alloy steels, a final tempering at 300℉ for one hour per inch of thickness is done; tool and stainless steels are tempered at a higher temperature appropriate for developing required hardness and other properties. After the final temper, the microstructural changes are complete. The resulting part is significantly stronger and tougher than the unprocessed component.
Benefits of cryogenic processing include:
• Increased resistance to abrasive wear
• Improvement of the properties of the core of the part, not just the surface
• Decrease in residual stresses while increasing toughness and dimensional stability
• Parts may be subsequently reground or machined without affecting the results of the cryogenic process.
While the applications for cryogenics at times appear to be unlimited, parts that benefit from the process include:
• Knives including cutlery, hunting, diving, survival, and general blades; also, metal shear blades. Cryogenically processed knives made from tool and stainless steels like A-2, D-2, and 400 series stainless steel hold their sharp edge longer than their untreated counterparts.
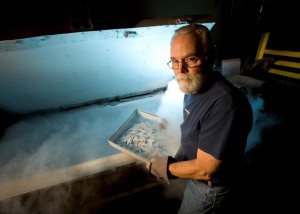
Operator removing a batch of cryogenically processed knife blades from a dry freezer prior to final tempering operation,
Blade Magazine, April 2012
• Forging dies – Cryogenic treatment of H-13 tool steel result in microstructural changes like fine martensitic structure, increase in carbide density, and uniform distribution, which improves hardness impact toughness, wear and stress rupture properties as compared to conventional hardened and tempered H-13 resulting in up to 25% longer tool life.
• Metal cutting tools like drills, taps, and dies, end mills, gear hobs, and broaches exhibit up to a five times improvement in tool life. Carbide tools also show enhanced performance believed to be from a shrink in the material filling in micro-voids between the tungsten carbide, titanium carbide, and/or tantalum carbide particles and cobalt binder. Medical and surgical tools and instruments also benefit from the process.
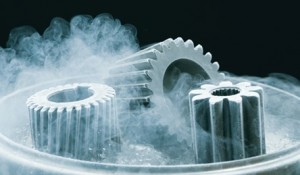
Courtesy, RE Music, September 2019
• Gears and bearings made from 8620, 9310, and 18CrNiMo6-7 are susceptible to premature failure if they are not cryogenically processed to convert retained austenite to tempered martensite.
• Automotive applications including brake rotors, transmissions, clutches, brake parts, rods, crankshafts, camshafts axles, bearings, ring and pinion, heads, valve trains, differentials, springs, nuts, bolts, washers are also beneficiaries of cryogenic processing. Enhanced performance makes cryogenics a staple of NASCAR, Formula 1, Drag Racing teams.
• Rock mining tools, specifically pistons, the key component in a hammer, are made from highly alloyed steels. Their repetitive impact against the drill bit in the tool makes them subject to high wear, chipping, and fatigue failures. Hammer pistons are carburized and hardened and then deep-frozen to improve tool life.
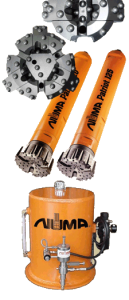
Hammers and drill bits for rock mining. The pistons located in the hammer are subject to repetitive impact against the bit, making them susceptible to failure by chipping or fatigue. Cryogenic processing of the pistons improves tool life.
Courtesy, NUMA Hammers and Bits.
It is important to note that cryogenics is not a substitute for heat treating but an enhancement. It adds a critical finishing touch to the heat-treating process. It has seen limited acceptance and use, mainly due to a lack of understanding of the technology. Except for the conversion of retained austenite to martensite, changes in other microstructural features are not visible with a standard laboratory metallograph. But changes in the lattice structure of the metals cannot be disputed; reduced residual stresses and the performance benefits of the process are well documented.
Metlab has extensive experience with cryogenic treatment for a wide variety of applications and can consult with you to provide the best solution to meet your product specifications.
Metlab prides itself on hiring and developing great employees. Metlab’s Facility Manager, Shane Parrish, was chosen as one of Heat Treat Today’s “40 Under 40” industry employees and was awarded the Heat Treat Industry Young Leader Certificate.
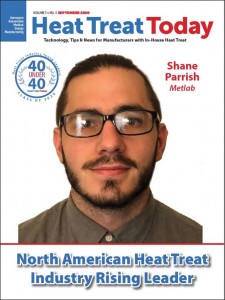
Shane Parrish, Facility Manager for Metlab, won the
Heat Treat Today’s 40 Under 40 Young Leader award.
Shane is an invaluable asset to Metlab. While attending engineering classes at night, he runs the maintenance operations in the plant, provides equipment modification ideas, and is a hands-on asset in keeping the plant running. He is an expert welder with creativity and skills and makes sure that the furnaces are safe and functional.
Shane has also demonstrated significant leadership by taking a lead role in plant safety by coordinating the safety committee and ensuring compliance with OSHA safe working practices. Shane’s knowledge of heat treating has grown significantly during his tenure with Metlab.
In high school, Shane developed a passion for designing equipment and projects on the computer using AutoDesk Inventor. Recently, Shane persuaded his company to invest in the program so that he could start designing upgrade projects for the facilities. Metlab also has many custom and old equipment, and their mechanical drawings are either out of date or unreadable. “With their investment in the program, I am reverse engineering the equipment here so that we have readable and usable mechanical drawings of the furnaces and equipment,” completing this work as an additional project to his in-house hours, he says.
Shane Parrish – Heat Treat Today 40 Under 40 award:
Shane Parrish – Heat Treat Today 40 Under 40
Heat Treat Today’s Complete 40 Under 40 list:
40 Under 40: Class of 2020
Metlab continues to build a successful business by providing quality heat treating and surface finishing services for its customers. To ensure this legacy, Metlab has recently hired Tom Guilliams as the Quality Manager for the company.

Tom Guilliams – Metlab Heat Treating’s new Quality Manager
Mr. Guilliams started with Metlab in June 2020 and brought with him extensive experience in Quality Control as well as metallurgical testing. He oversees a wide range of processes and procedures, including production planning and material management.
“I manage with understanding and frequent communication,” Guilliams comments. “Engaging everyone in the Quality program requires patience. It is a learning process that I share with others, and it is an essential part of the continuous improvement process.”
Changes have already been implemented to enhance the quality focus throughout the organization:
• The Quality Manual is being reviewed and updated to bring the organization up to the 2015 ISO standard.
• The Calibration Log was updated: “one over one” certification review implemented to ensure accuracy.
• “Going Paperless” by using electronic communications for quality certifications instead of printouts and mailings.
Another area for improvement and change is in the testing lab. “I have a laboratory background and extensive connections in the testing field,” Guilliams notes. “Metlab has testing capabilities; however, we also use third-party labs for testing. I’m able to find the best labs for the most accurate testing, which are faster and less expensive.”
Part of the continual improvement process is training. Guilliams elaborates, “We provide company-wide training so that everyone understands the importance of quality. We have daily conversations about expectations and limitations. My job is to grow people as well as the business. We make sure that the customers are taken care of by having a customer-facing quality program in place throughout the entire organization.”
|