Metlab recently black oxide finished a suit of armor for an artisan. The armor was manufactured by M & M Metals of Jeffersonville, PA. The complete suit of armor consists of about 125 hand-formed metal plates, and will cover and protect the wearer from head to toe.
Robert (Mac) McPherson, owner of the business and manufacturer of the armor has been handcrafting suits of armor since the late 1970’s, and is considered among the best in the world.
The armor is based on a late 15th-century statue of St. Florian (patron saint of firefighters) in a German church. While the form and detail of the armor in the statue were retained, the proportions had to be altered to fit the customer, who is a tall man with a “mature figure”. Mac spent many hours forming 1050 medium carbon steel sheet into the various components that comprise the suit. Each plate was shaped using only hand tools, and was then hardened and tempered. Afterwards, each individual component was ground and polished. Blackening this suit of armor represented the culmination of many months of work.
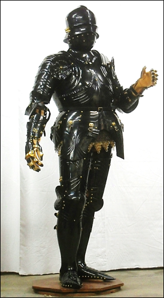
Black oxide imparts a deep, black, lustrous appearance
to the parts being coated and replicates the surface finish of the part.
The modern black oxide coating that Metlab applied to the armor is very durable and attractive. Black oxide finishing is offered in addition to the current array of heat treating services. Black oxide is classified as a conversion coating. The black oxide processing of the armor consisted of taking individual pieces and placing them in large work baskets and running the baskets through the black oxide line. About eight individual cycles were required for the parts. The process, characterized as a “hot black oxide process” is carried out at 265°F to 285°F. After blackening, the parts were coated with a dry-to-the-touch oil and then hand wiped to remove excess oil, providing the pieces with a lustrous, glossy finish.
It may seem strange that there is any market for medieval armor, but the demand is greater today than it has been for centuries. Worldwide, there are tens of thousands of medieval reenactors in numerous different organizations. While many dress in their armor for “living history” events (imagine Civil War reenactors, but set them a few centuries earlier) most of them fight in some sort of tournaments. Some organizations compete with wooden weapons and others use blunted and edgeless steel ones. Most of these tournaments, melees, and “wars” are fought on foot, but some are done from horseback. There is currently a large and growing jousting scene.
Jousts range from the choreographed spectacles with breakaway lances that one finds at Renaissance Faires and medieval-themed dinner theaters to competitive jousts using solid lances with steel heads. There is also a niche for the modern armorer who makes high quality armor for collectors.
This is the second suit of armor that Metlab has blackened for M & M. The first suit was done over 10 years ago, and that armor was based on English effigies (tomb sculptures) and artwork of the mid-15th century. In addition to what is shown in the picture, the armor included another helmet, two additional visors, and a steel plated saddle. The owner not only cut an impressive figure, but has jousted very successfully in the armor.
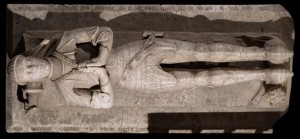
Effigy of Sir John Cressy, from which most of the details of his armor came from. Photography by Cameron Newham.
Historically, most armors were polished bright, and left “white”, but many were blackened, russeted, or blued. Sometimes these colors were built up by slow rusting, like antique firearms. This produces a brown or black color depending on whether the steel is steamed. Other times, the armor was made a shade of blue or purple by controlled heating. This is like the color one sees on antique watch hands. Another common method of creating a black finish was to bake on a coat of oil, like seasoning a frying pan. These methods can produce an attractive color and some degree of rust prevention.
In addition to suits of armor, Metlab uses its black oxide process in a variety of industrial applications in widespread industries. Some examples include:
• Retail: Store displays and fixtures.
• Automotive: Cans for oil filters, numerous under the hood fasteners
• Electrical: Wire strippers and cutters
• Home / Garden: Tree toppers – jaws and clipping tools
• Gearing: Small gears for tiny timers and electrical switches
• Firearms: Gun components, shotgun shell magazines
Metlab has complete heat treating capabilities along with extensive experience to provide consulting for complex and unique projects and applications.